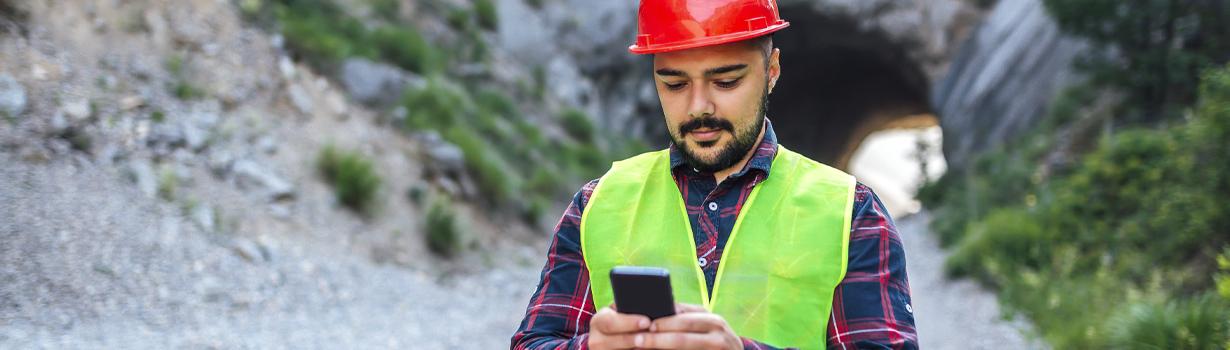
WASTEWATER POND DESLUDGING
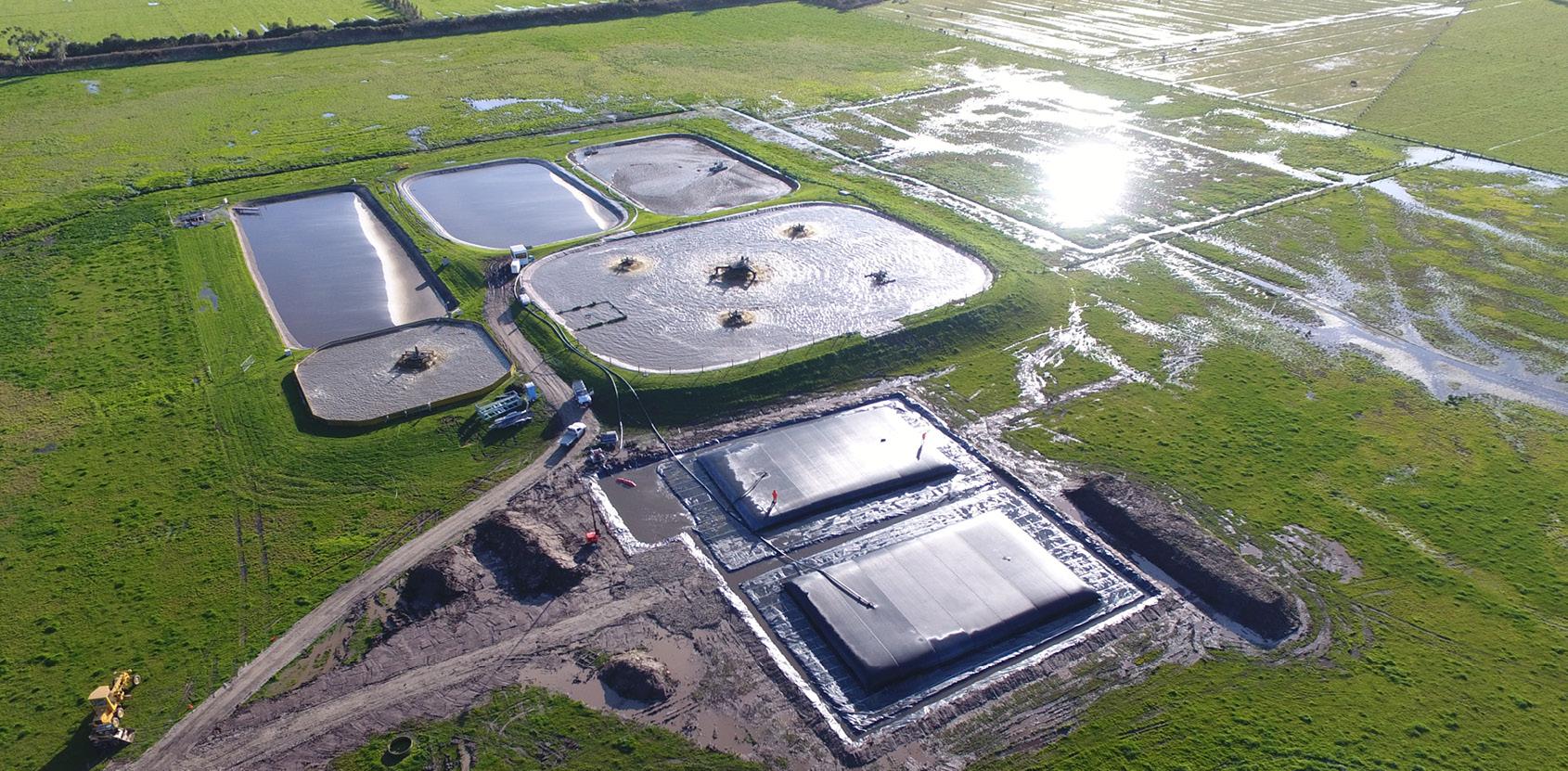
PROJECT DESCRIPTION
Dredging Services was engaged by a meat processing facility in regional Victoria to carry out the cleaning and desludging of three wastewater ponds with a combined capacity of 12ML.
Over the years, the ponds had built up with solids which had settled to the floor, taking up a percentage of the pond capacity.
The supernatant clear water on the pond surface is traditionally either evaporated off or used on site for irrigation, while complying with Environment Protection Authority (EPA) regulations.
Without regular cleaning and desludging, ponds will eventually become full of solids meaning that waste can no longer be pumped into the ponds.
The mind set of constructing new ponds as a solution is changing as we continue to develop more economical methods to dewater sludge. We’re also finding new environmentally friendly uses for the dried solids without disposing direct to expensive waste facilities.
CHALLLENGES
Dewatering biosolids often encounters three common issues:
1. Solids variability: The variability in the solids type means a varying dose rate which can cause difficulties in flocc management. This can be managed by experienced operators
2. Gas: Methane is a by product of the biosolids and can be generated once the dewatered solids are in the TenCate Geotube®. This can cause some unwanted inflation in the units but can be managed by an experienced operator. In this case, Geofabrics were available to discuss projects and methodologies from past experiences
3. Fats and Grease (FOGs): FOGs are quite rare, but more common with biosolids. It can create geotextile clogging concerns and slow dewatering times. Traditionally FOGs are more difficult to flocculate and without the proper experience from a polymer expert or a dredging operator it can blow project timelimes out considerably.
Biosolids are also difficult in terms of waste disposal, but there are options for them once dried:
- The dried solids remain on site, the bags are cut open and the solids are spread as fertiliser
- Solids can be disposed of as waste film, but this can be highly expensive depending on the location
- It can be disposed as compost, which can be cheaper than waste fill disposal depending on location
- It can be sold as fertiliser to an end user direct. This is obviously the most financially viable option and is becoming more acceptable, but the EPA may require checks.
Geofabrics were initially engaged to provide guidance on the most economical configuration for TenCate Geotube® dewatering units, and we provided recommendations for the dimensions for the level dewatering platform.
Mark Henderson of Mr Henderson Water was also engaged to provide expert advice with respect to the polymer dosing and flocculation of biosolids.
Flocculation using a suitable flocculant or polymer is the key to success with TenCate Geotube® technology, particularly when dealing with biosolids.
Coagulants are traditionally not adequate to produce a “flocc” large enough to dewater through the geotextile effectively and quickly.
They’re known to combine the colloidal matter which helps to produce clean water but are traditionally not enough on their own.
OUR SOLUTION
Once all the upfront planning was complete, Dredging Services were able to commence the dredging of sludge into the bags but not before mixing it with the chosen polymer.
The TenCate Geotube® units were pumped to maximum fill height and the flow was diverted to the next TenCate Geotube®, or the pump was switched off to allow passive dewatering to continue.
The pump cycling was continued until the bags were considered full and to have removed a majority of solids within the ponds.
The project took approximately four weeks to complete, and the units were left to passively dewater for a period of one to two months until the material is spadable.
The Geofabrics team were always on call to field questions from the team on site, creating peace of mind for the operator and ensuring any hurdles could be managed.
Geofabrics hold standard TenCate Geotube® stock levels within Australia, ensuring project timelines can be met. For larger projects, custom units can be made to fit certain footprints or for stacking requirements. In this case, a short 5 to 6 week lead time can be expected.
PRODUCT USED
Solmax Geotube® Dewatering Container Geotextile
- Used for sludge dewatering projects of all sizes and there is good reason - simplicity and low cost
- On this project the GT500-366-306-B2P08 units were used, which are manufactured from GT500 woven monofilament and fibrillated geotextile, which is made using a propylene yarn meaning it is inert to most water chemistries
- These particular units can store up to 1,000m3 of material, being 30.6m long by 18.3m wide when laid flat and the circumference of the bag is 36.6m with each unit containing 2x200mm PVC flange filling ports
- They have a very high seam strength to allow for high pump heights, which in turn create larger volumes per sqm of footprint and induce a higher factor of safety during pumping
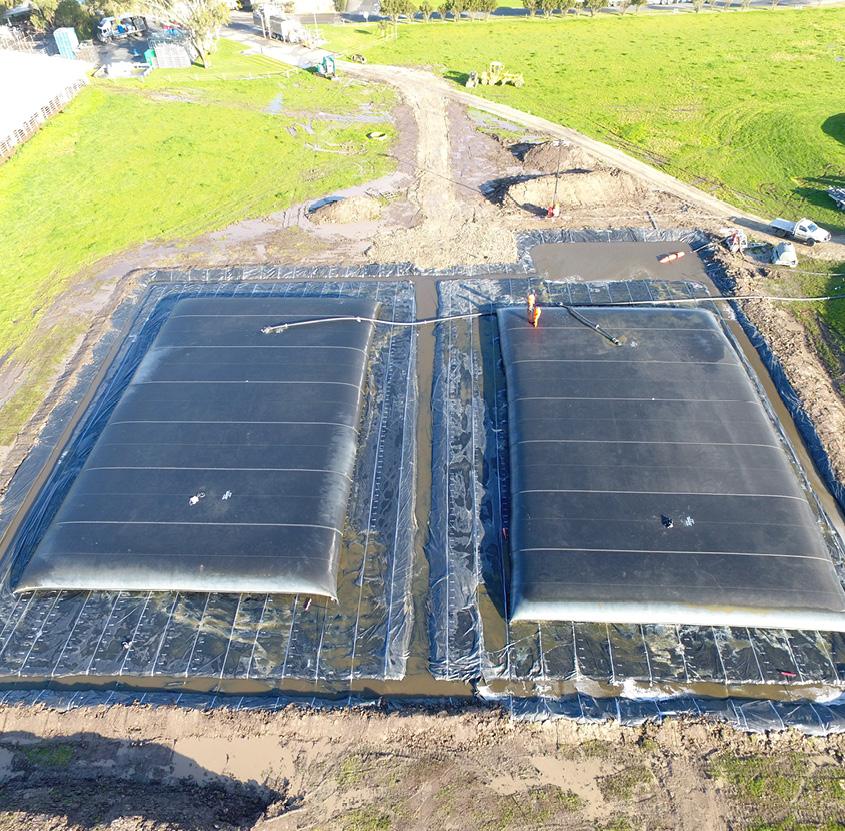
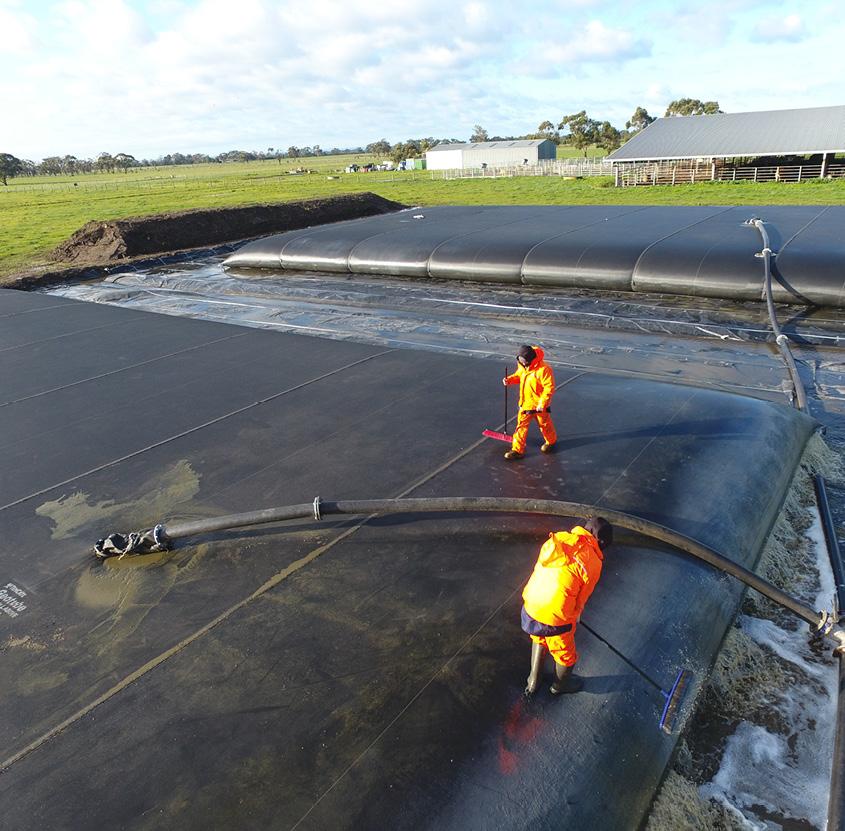