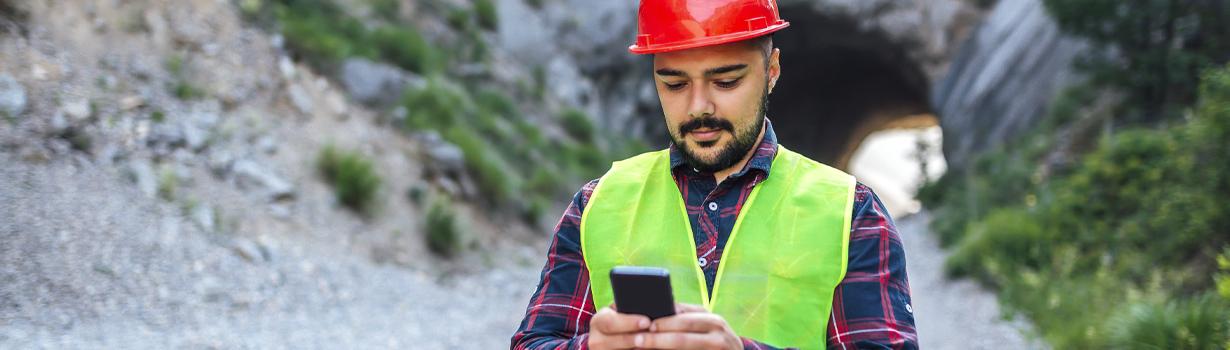
Tracktex Turnout
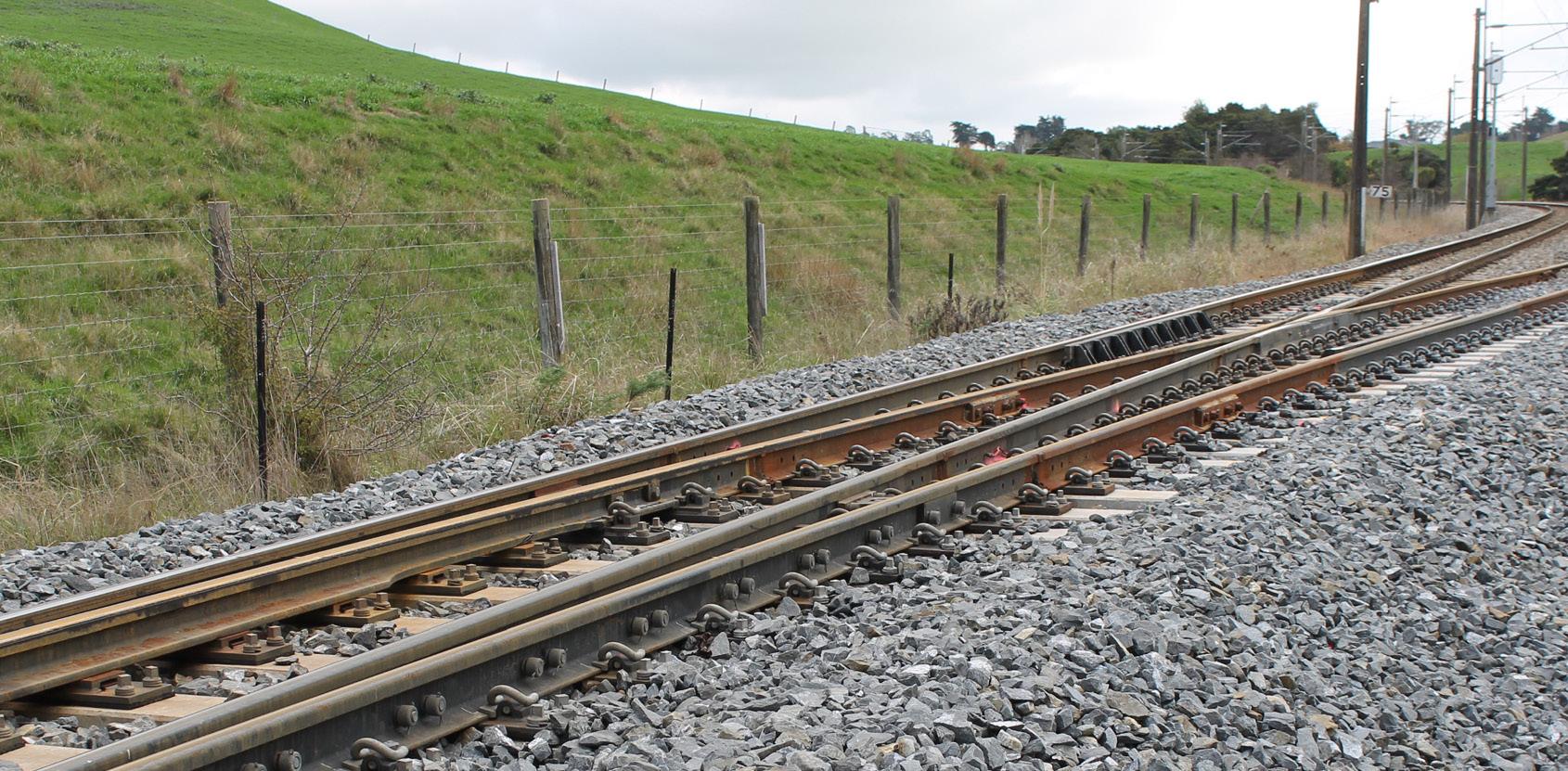
Mud-spots are a common occurrence along sections of railway throughout New Zealand. These are areas where water accumulates and causes contamination and wear of the ballast by movement of the particles. The first section of rail, North West of Feilding is a turnout intersection (Maewa site which has a history of being wet) and is prone to mud spots and subject to repeat visits for maintenance.
Geofabrics provided installation guidelines and technical information to the client. A Geofabrics New Zealand Ltd local area representative provided on site assistance until the installation was complete
Installation followed the same procedure as the Woburn and North Street sites previously completed - overhead power was turned off after the last train went through. The Maewa site (done on Taranaki Anniversary) involved Udy Construction and KiwiRail staff with the removal of 34 m of track including the turnout. Power and signal connections were disconnected, and the section of rail cut in four sections for removal. The old ballast was then removed with two, 12 tonne diggers, and the subgrade undercut by another 200 mm to get to firm foundation. A 150 mm layer of crushed AP40 was then compacted by a three and a half tonne roller. A drain was formed on the southern side and 160 mm Novacoil with a filter sock was placed into the drain prior to being covered by a layer of ballast.
Tracktex was then placed on the prepared subgrade, with overlaps of 1.5 m, Tensar TriAx170 then placed directly on top followed by a 300 mm layer of 40-80 mm ballast. Replacement sections of new rail and concrete sleepers (four sections each 14 tonne) were then replaced and re-welded together, followed by top up ballast to final level.
The removal of track, site preparation, product installation, new ballast and track installation were done over approximately five hours. Due to other delays the line was reopened approximately six hours later. The installation of Tracktex and Tensar TriAx 170 went smoothly and the client found it a quick process.
This site will continue to be monitored and mud-spots should now be minimised with no need for return maintenance visits.
The preparation is required whether maintenance, rework, or installation of products is required. The contractors found this is an easy product to install and compared to traditional sand layers, was quick and simple. This resulted in savings for the client, due to down time on the main lines being kept to a minimum.
DOWNLOAD THE CASE STUDY