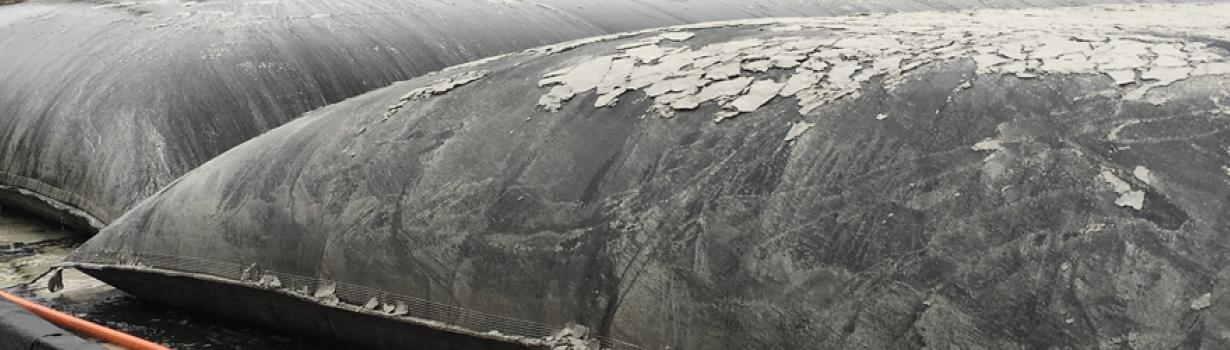
Sludge Dewatering VIC
Our client manufactures superphosphate at an Australian plant.
A byproduct of superphosphate manufacture is formation of silica in fluorosilicic acid (H2SiF6). The silica and acid, along with any entrained superphosphate dust is captured in the process ponds for storage, these ponds also include the wastewater runoff from around the facility to ensure no product ends up in the local waterways.
Solids need to be removed to restore storage capacity as the pond is not agitated and just continues to build up, the last time these ponds were cleaned out was approximately 10 years ago, Geotube Dewatering Containers were used then also, due to the corrosive nature of the acid and messiness of the product. Geotube Dewatering Containers have proven to be the most efficient, safest and cleanest method of removing the solids, with a key factor being they can carry out the process during normal operation and did not disrupt plant operations.
The objective of the project was to separate the solids in the process pond (primarily silica and superphosphate) from the liquid (approx 20% fluorosilicic acid). Sludge was supplied from the pond via a sludge pump, solids were suspended in the sludge using an aeration wand. The solids removed were then recycled back into the product, while the liquid was either bled back into the process or treated. In order to return the solids back into the process the level of moisture content in the solids had to minimized, this was achieved by the drying time in the Geotube which is typically around two to three weeks and when they were ready the contents were removed via loader into covered storage for final drying and secondary conditioning.