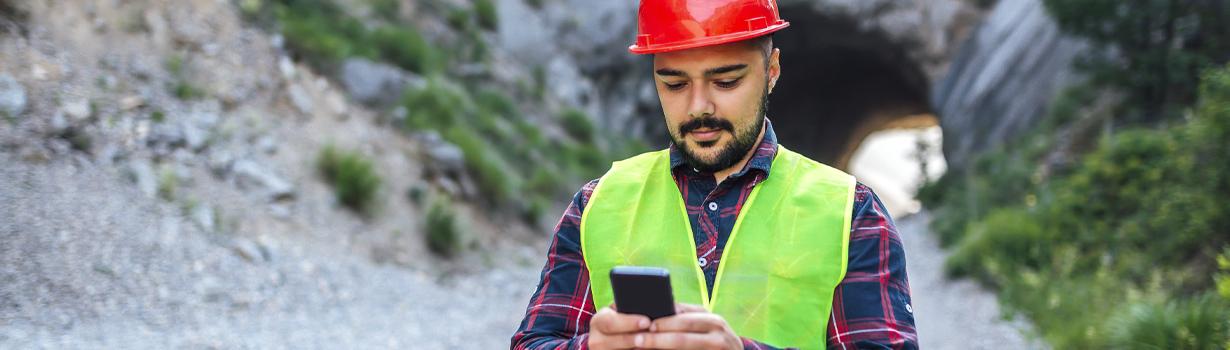
IRRIGATION CANAL LINING WITH CCX IN EGYPT
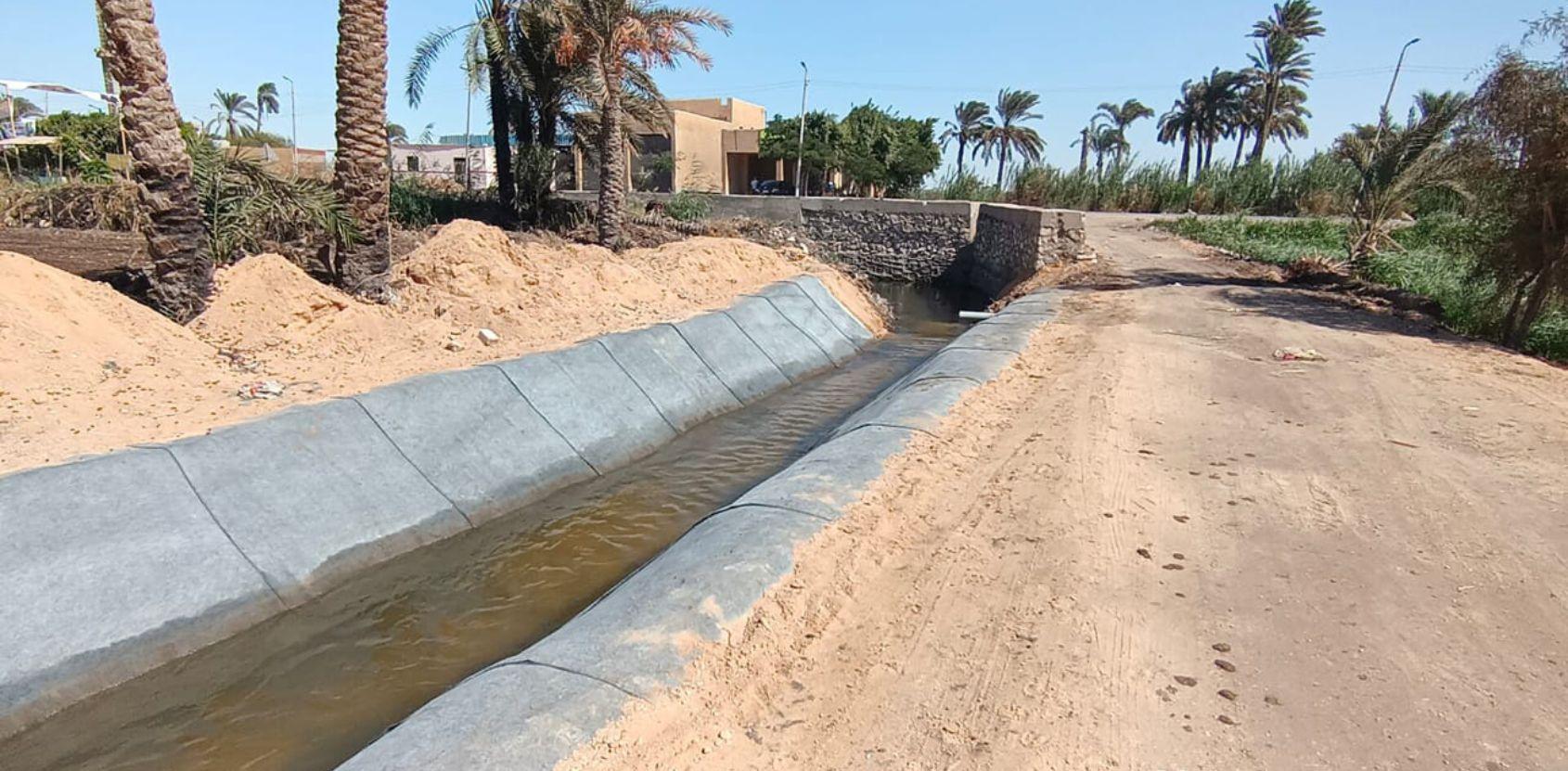
PROJECT INTRODUCTION
In September 2020, Concrete Canvas CCX-B™ (CCX-B™) was installed on a trial basis at a site in Atfih, Egypt. The objective was to provide a rapidly installable, non-erodible and impermeable lining solution for an existing unlined irrigation canal.
The section of canal being lined measured 50m in length, with an invert width of 1m and an average side slope measurement of 3m at a 1:1 slope.
CCX-B™ was installed by Geotech (the official Egyptian partner for Concrete Canvas Ltd) & Samco (Geotech’s parent company) for the Egyptian Ministry of Irrigation, with guidance and support provided by a representative from Concrete Canvas Ltd on site.
BACKGROUND
The Egyptian Ministry of Irrigation are currently carrying out a scheme to extensively upgrade their network of irrigation canals from earth lined to concrete lined.
At present, the majority of canals in Egypt are unlined, resulting in more than two-thirds of the water conveyed being lost to seepage.
The existing specification for lining the canals is the creation of a formation layer with 300mm thick un-grouted rock. On top of this, a layer of geotextile is placed, followed by a 100mm thick skin of 20Mpa concrete. This three-stage process is very time consuming to install and does not incorporate the use of a geomembrane. It is also prone to differential settlement panel movement and cracking with a resultant significant increase in permeability and water loss again to seepage.
CCX-B™ was awarded a trial at Atfih to demonstrate its speed of installation and impermeability that ensures water tightness and maximises the capacity of the canal. CCX-B™ also has a much greater differential capacity making it more suitable to expansive soils. The composite nature of CCX-B™ is therefore capable of replacing all three elements of the existing specification in one application.
SITE CONDITIONS
The condition of the existing canal was very poor on initial inspection. When the canal was drained to carry out a detailed inspection, it was revealed that significant erosion of the sides, as well as deposition of sediment and waste on the floor had occurred, drastically reducing its capacity and functionality.
The design profile of the canal required reinstatement prior to lining. This was accomplished by first cleaning out the deposited sediment and then tipping in an imported gravel. The gravel was compacted in layers to the top of the slopes and then the canal profile excavated from this. Once the profile excavation was completed, the invert was re-compacted to create a sound working surface.
Anchor trenches were excavated by hand 300mm from each canal shoulder, measuring 200mm deep by 300mm wide, allowing for a CCX-B™ run-out of 100mm.
In terms of climatic conditions, the site location is very hot year-round with average daily temperatures of between 35 and 40 degrees Celsius at the time of the trial. During September it is also common to have significant drying conditions due to wind which prevailed during the course of the trial.
INSTALLATION OF CCX
Installation began downstream, with the CCX-B™ rolls laid transversely across the channel profile, working in an upstream direction. The rolls, which measured 10m or 20m long and 2m wide, were lifted on a spreader beam by a 10-tonne excavator and the material drawn off by hand. Once laid in place, the CCX-B™ was cut to length with a disc cutter and temporarily pegged within pre-prepared anchor trenches to prevent movement. Subsequent lengths of CCX-B™ were laid so as to overlap the preceding panel by 100mm, with overlaps oriented in the direction of water flow.
In order to joint layers of CCX-B™, the top cement filled geotextile laps were folded back to reveal the underlying LLDPE geomembrane backing. The geomembrane is overlapped to create a 100mm wide lap. The geomembrane backing can then be bonded using either a Leister Twinny double track welder or a Leister Triac hand held hot air gun and roller.
Once the geomembrane had been welded, the cement filled geotextile overlaps were folded back, one over the other, to create a 100mm wide protective lap. These overlaps are fixed either by thermally bonding the layers with a Leister Triac or by adhesion. Both methods were trialled on this installation, with adhesion provided by applying two 10mm diameter beads of adhesive sealant parallel to the geotextile laps at a distance of 30mm and 70mm from the overlapping edge. Thermal bonding was achieved with a 60mm perforated nozzle.
Once jointing was completed, the edges were secured within the anchor trenches using an anchor peg and hydration commenced.
Due to the high ambient temperatures on site, in combination with a moderately dry wind and CCX’s initial setting time, it was critical that hydration was carried out sufficiently and systematically. It was determined that a staged approach of three rounds of hydration be conducted, initially at 15-20-minute intervals and then a final hydration given to saturation approximately 1 hour later. Following hydration, anchor trenches were gravel backfilled and hand-compacted.
The installation progressed at a rate of approximately 75sqm per hour and was completed within half a day.
PERFORMANCE TESTING
In order to determine the performance and long-term efficacy of CCX for this trial, post-installation tests were carried out to:
- De-silt the CCX lined canal with a mechanically operated bucket
- Carry out a patch repair of a small section in case of future damage caused by operator negligence
- Conduct a laboratory test and analysis of the water cement ratio and flexural strength of CCX-B to ASTM D8030 and ASTM D8058 respectively.
De-siltation by mechanically operated bucket was carried out successfully without any damage caused to the lining. A patch repair was also carried out successfully to a purposefully created small puncture of the CCX-B lining. A detailed repair methodology was then drafted accordingly for future use.
PERFORMANCE OUTCOME
The trial was successful and is currently under consideration by the Ministry of Irrigation for incorporation as an approved alternative to their current lining specification. It fulfilled all the prerequisites of the Ministry of Irrigation in terms of speed of installation, impermeability and maintenance.
The 50m length of canal lined with CCX-B™ is noticeably more efficient than the unlined section positioned upstream and downstream. CCX-B™ provides a more durable, erosion resistant and impermeable solution than that currently incorporated on the canal network and is fit for purpose for all future canal linings of similar terrestrial conditions.
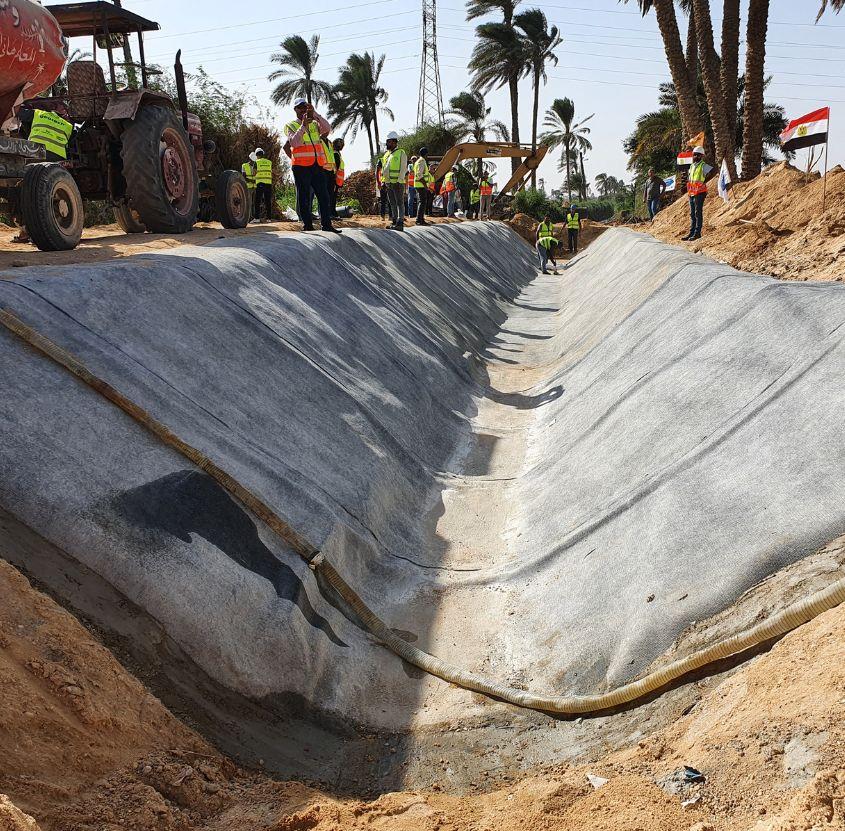
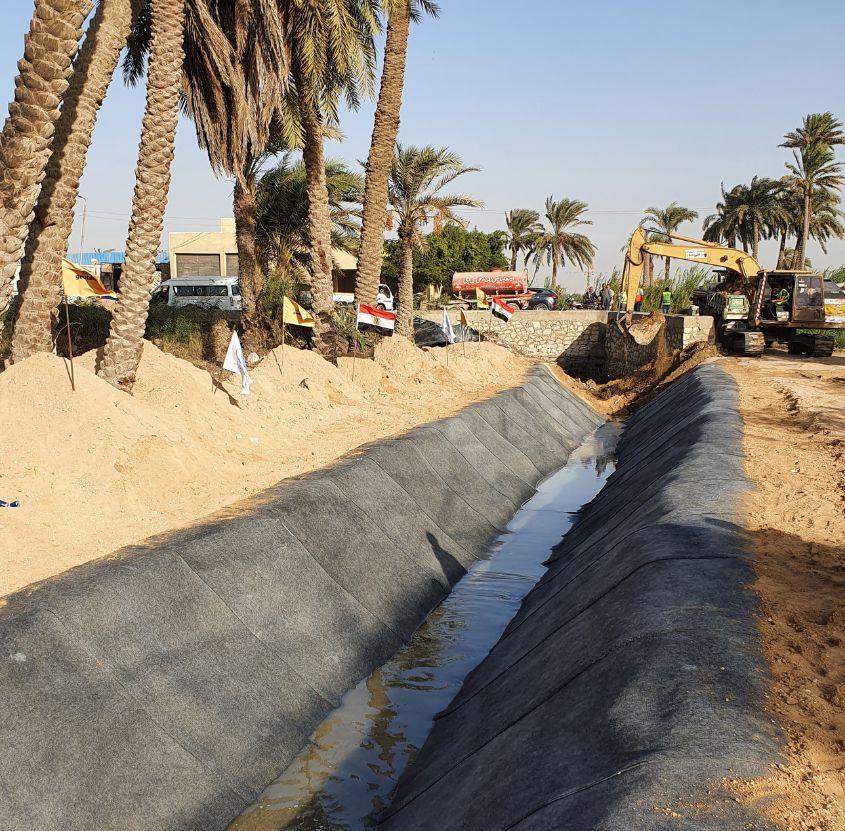