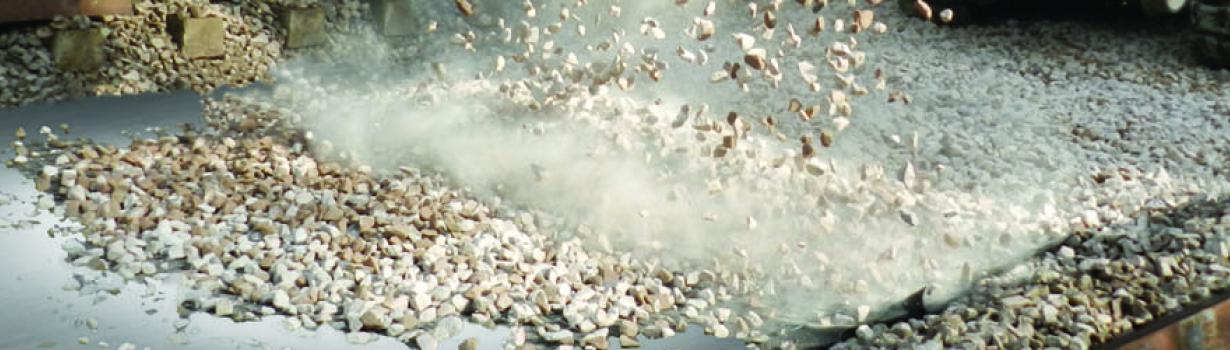
Heavy Load Train Line Track Renewal Works
Much of the 40,000km of rail track traversing our great Australian land was constructed at a time when minimal engineering input was considered and therefore much of it is built upon low quality formations which over time has settled, deformed and lost much of its load bearing capacity. As well as this, rail loads have increased significantly with Rail Authorities increasing the axle loads of their rollingstock to facilitate the transport of heavier freight loads.
The standard repair method for poor performing sections of track is to excavate the contaminated or unsuitable material and replace them with imported better quality granular foundations. However, contemporary research and infield experience over the past 30 years has shown that utlisation of geosynthetics within the formation can deliver whole of life cost reductions of up to 50% as the solutions deliver both construction cost savings and increased maintenance cycles.
Geofabrics recently assisted a client whose heavy load rail line was constructed on unconsolidated soft formations which had resulted in unacceptable settlements, leading to temporary speed restrictions being applied to the track.
A 125 m section of track formation was required to be renewed and Geofabrics were requested to provide suggestions using Geosynthetics. The intention of the inclusion of geosynthetics was to minimize the required construction timeframe and thereby reduce the impact on the rail operations. The exact problems being encountered were unconsolidated soft formations of CBR 3 and 15% moisture content, unacceptable settlements and speed restrictions. The design requirements of the renewed section needed to achieve a 20 year design life at 80 km/hour speed.
Geofabrics worked in conjunction with it’s leading Geosynthetic Industry partners to provide design solutions and the accepted option resulted in maximum savings in excavation, imported material and construction time. The solution was to place a multi-layered high strength woven geotextile immediately on the excavated surface upon which a 150 mm deep Geoweb cellular confinement system was placed. The Geoweb panels were joined using the patented Atra Key system and then secured with Atra Anchors. Once the Geoweb was expanded and secured, it was infilled with a capping layer material which exceeded a CBR of 50 and overfilled by approx. 100mm to allow compaction equipment to drive directly on it and compact it to the required specification. Once compaction was achieved the resulting cover over the top of the Geoweb cells was approximately 50 mm.
To further enhance the longevity of this renewal, the Client adopted the suggestion of placing an Anti-pumping geocomposite, Tracktex, directly on the compacted capping layer and then combined it with a specifically manufactured “ballast” geogrid. The Tracktex will prevent the ingress of rainwater through the ballast and into the newly confined capping layer thus protecting it from ongoing degradation and also preventing any pumping of the finer fractions of the capping layer into the ballast layer. The “ballast” geogrid, Tensar TX190L, was included to stabilize the 300 mm ballast layer by restricting ballast movement and settlements.
Studies have shown that the inclusion of Tensar TX190L in the ballast works by stabilizing and restricting ballast movement by up to 300 mm above its interface. In addition, it has been demonstrated that it can significantly reduce ballast breakdown under heavy loading conditions which in turn minimizes the rate of ballast deformation and fouling. This obviously reduces tamping cycles.
Geofabrics worked closely with the client on this project renewal by providing design suggestions, technical advice and representation on site during installation.
This cost effective geosynthetic solution provided the client exceptional value for money and superior technical performance by minimising subgrade excavation, importation of sub-ballast capping material and construction time on site. The 125 m track formation renewal project was completed within the allocated shutdown window with minimal disturbance to train operations.
DOWNLOAD THE CASE STUDY
Heavy Load Train Line Track Renewal Works