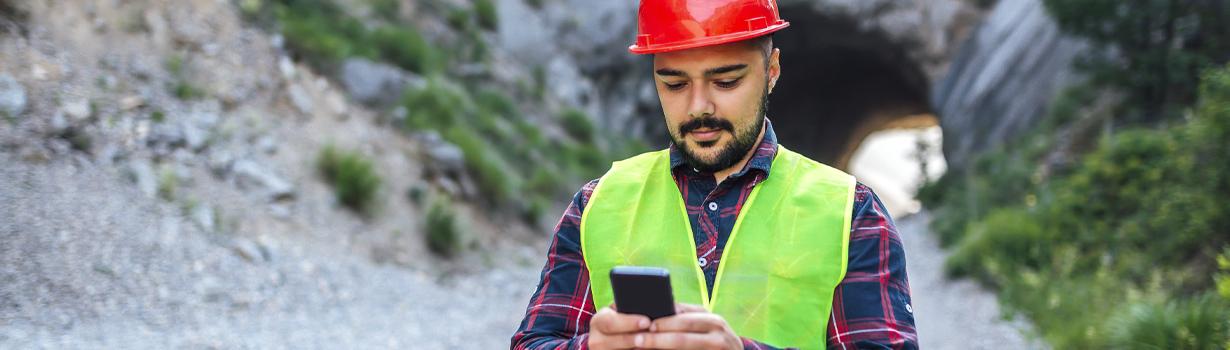
STABILISING AN ACCESS ROAD WITH MIRAFI RSI
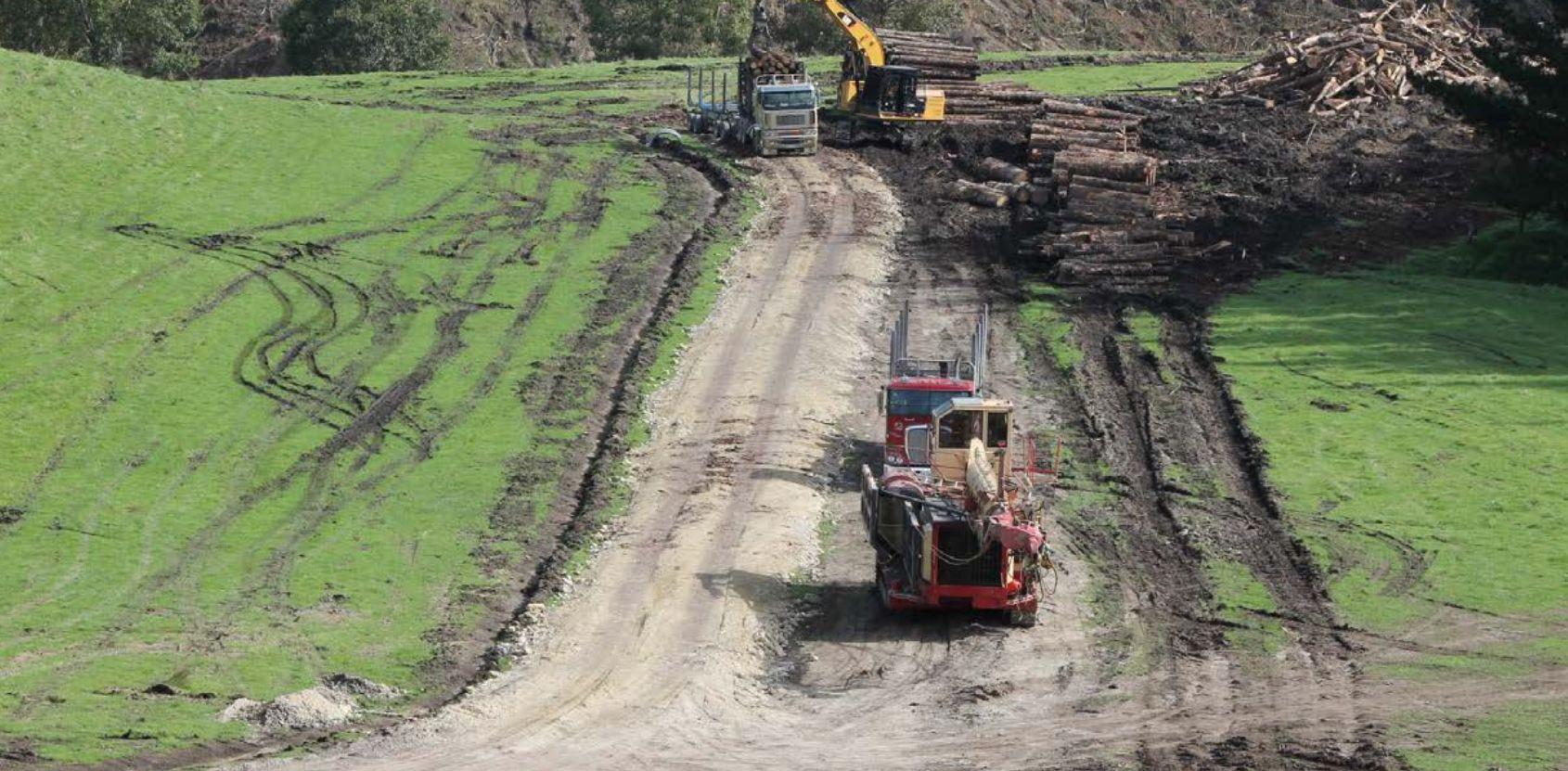
A forestry access harvest road was required into a private block in Glengarry, Hawkes Bay. Due to the recent storms (cyclones Debbie & Cook) access had become very difficult at the final stage of the road construction to access the final 1400 tonne of logs left on the landing after the crew had finished.
Usually, if corduroy is available, this is placed on the existing surface and then covered by the roading aggregate. In this instance the surface and subgrade was saturated which meant the aggregate was disappearing as fast as it was being placed.
Even corduroy where it was used was sinking into the existing surface. A cost comparison was made by the client, to continue putting in aggregate or to use the Mirafi RS380i with new aggregate. The $15k difference calculated was significant with $11k the cost with the geotextile vs $26k if metal continued to be applied on its own.
Geofabrics New Zealand Ltd had previously left Pan Pac a sample of the Mirafi RS380i, its benefits and applications had been explained. In this instance there were several factors, the new road was to be placed parallel to the existing road (uphill side) in a ‘Greenfields’ situation (undisturbed), and the aggregate that was to be used was straight haul 300 mm limestone (this later increased to up to 500 mm). Usual geotextile and geogrids can accommodate up to 75 mm, but this grade is usually at a premium price. The Mirafi RS380i due to its unique manufacturing properties made this an ideal candidate, as well as the increased width ideal for forestry roads with a carriage width of 4.6 m.
The length of roading required was approx. 240 m, including a turning bay near the start, so that the trucks could be backed down to the loading site. The rolls were 100 m length, easily rolled out by 2 or 3 people, and easy to shift if required. While walking on it, the water was coming through the fabric immediately, showing the porous nature of this woven polypropylene filament product.
Old limestone aggregate off the old road was recovered (minimising any topsoil) and placed on top of the Mirafi RS380i to keep it in place until the limestone aggregate could be placed. Any overlaps where required were done at 1 m. Trucks with approx. 6-8 m³ were then backed down the access road and emptied at the end of the spread aggregate. A 20 tonne excavator then spread the aggregate while sitting on it, to a thickness of approx. 200 mm which was then compacted by the excavator. The 240 m was covered in approx. 2 days (16 hours approx.). Once completely covered, the road was then accessed by logging trucks. After initial repeated trafficking ruts formed, a levelling of the aggregate to fill the ruts was required, after this minimal maintenance was required.
Areas that had some excess topsoil in the recovered material were removed and replaced with clean cover aggregate. Forty truck and trailer units (50 t gross weight fully loaded) then utilised this road over a two-day period until all logs had been removed. The 35 tonne log loading excavator when accessing the site left significant track marks on the Greenfield area, rainwater is still sitting in these tracks as the cooler weather and lack of wind has meant minimal drying weather over the period.
Both the excavator and log loading digger operators commented that this product had worked exceptionally well and without it the client would not have been able to recover the logs without significant cost by other methods.
Since the installation on this site the Mirafi RS380i has also been used on another site using up to 300 mm aggregate, and no issues were encountered. This is likely to be used on other difficult sites that are hard to enter during winter, especially on private blocks to be harvested where the roading network has to be established from nothing and can use the cheaper larger straight haul aggregate.
PRODUCT USED
- Superior separation and filtration capability with effective prevention of aggregate mixing and loss of sub-base material into soft subgrade
- Material cost savings of up to 33% by reducing the amount of base material required
- Unique double layer construction provides a wide range of pore sizes for an excellent separation factor, superior filtration and flow characteristics of a fine to coarse sand layer
- Excellent soil and base course confinement resulting in greater load distribution
- Robust structure that withstands the effects of rough dumping and filling with minimal damage
- High permeability with efficient release of pore water pressure which makes it suitable for installation over soft wet soils
- Easy installation by simply laying and aligning the system